Case Study
How Nando’s improved operational efficiency of their 120 kitchens by switching to a centralised maintenance system
Baker Group AU introduced a consolidated maintenance approach to streamline kitchen equipment maintenance across 120 sites for Nando’s. With in-house, dual-trade technicians trained by Original Equipment Manufacturers (OEMs), Baker Group also ensured that all work met manufacturer standards.
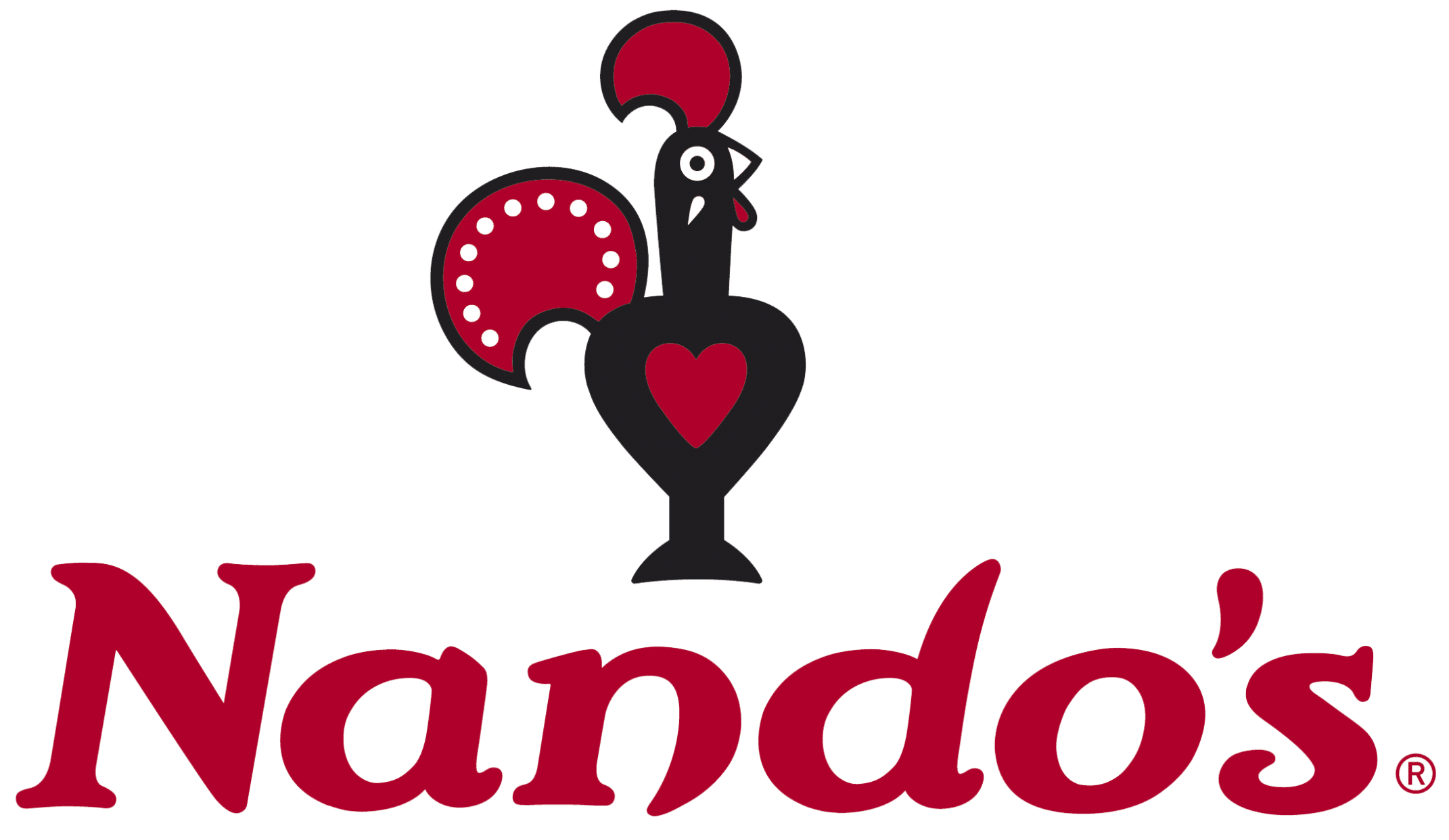

Since partnering with Baker Group AU in June 2024, our kitchen maintenance has become so much more efficient. We used to juggle multiple contractors, which meant higher costs and too many service calls. Now, with Baker Group managing all 120 locations, everything runs smoother.
They’re proactive, quick to respond, and work directly with our OEM suppliers to ensure top-quality servicing. It’s taken the stress out of maintenance, saved us money, and kept our kitchens running without a hitch.
They’re proactive, quick to respond, and work directly with our OEM suppliers to ensure top-quality servicing. It’s taken the stress out of maintenance, saved us money, and kept our kitchens running without a hitch.
Warren Carlyle
Asset and Property Manager Operations, Nando’s ANZ
The Challenges - uncontrolled costs, broken communication and inconsistent service quality.
Nando’s Australia’s reliance on multiple contractors for maintenance created a trifecta of issues that negatively impacted their operations.
Uncontrolled costs: The most pressing issue was the financial strain of inflated service fees. Juggling multiple contractors meant dealing with multiple invoices and potentially overlapping charges, driving up overall maintenance costs.
Broken communication: Communication breakdowns were another significant problem. Coordinating with various contractors resulted in fragmented communication, making it difficult to track work orders, resolve issues promptly, and maintain clear lines of responsibility.
Inconsistent service quality: Finally, the lack of a centralised maintenance provider led to inconsistent service standards. Different contractors brought varying levels of expertise and adherence to Nando’s operational efficiency standards, potentially impacting the customer experience and overall brand image.
Uncontrolled costs: The most pressing issue was the financial strain of inflated service fees. Juggling multiple contractors meant dealing with multiple invoices and potentially overlapping charges, driving up overall maintenance costs.
Broken communication: Communication breakdowns were another significant problem. Coordinating with various contractors resulted in fragmented communication, making it difficult to track work orders, resolve issues promptly, and maintain clear lines of responsibility.
Inconsistent service quality: Finally, the lack of a centralised maintenance provider led to inconsistent service standards. Different contractors brought varying levels of expertise and adherence to Nando’s operational efficiency standards, potentially impacting the customer experience and overall brand image.
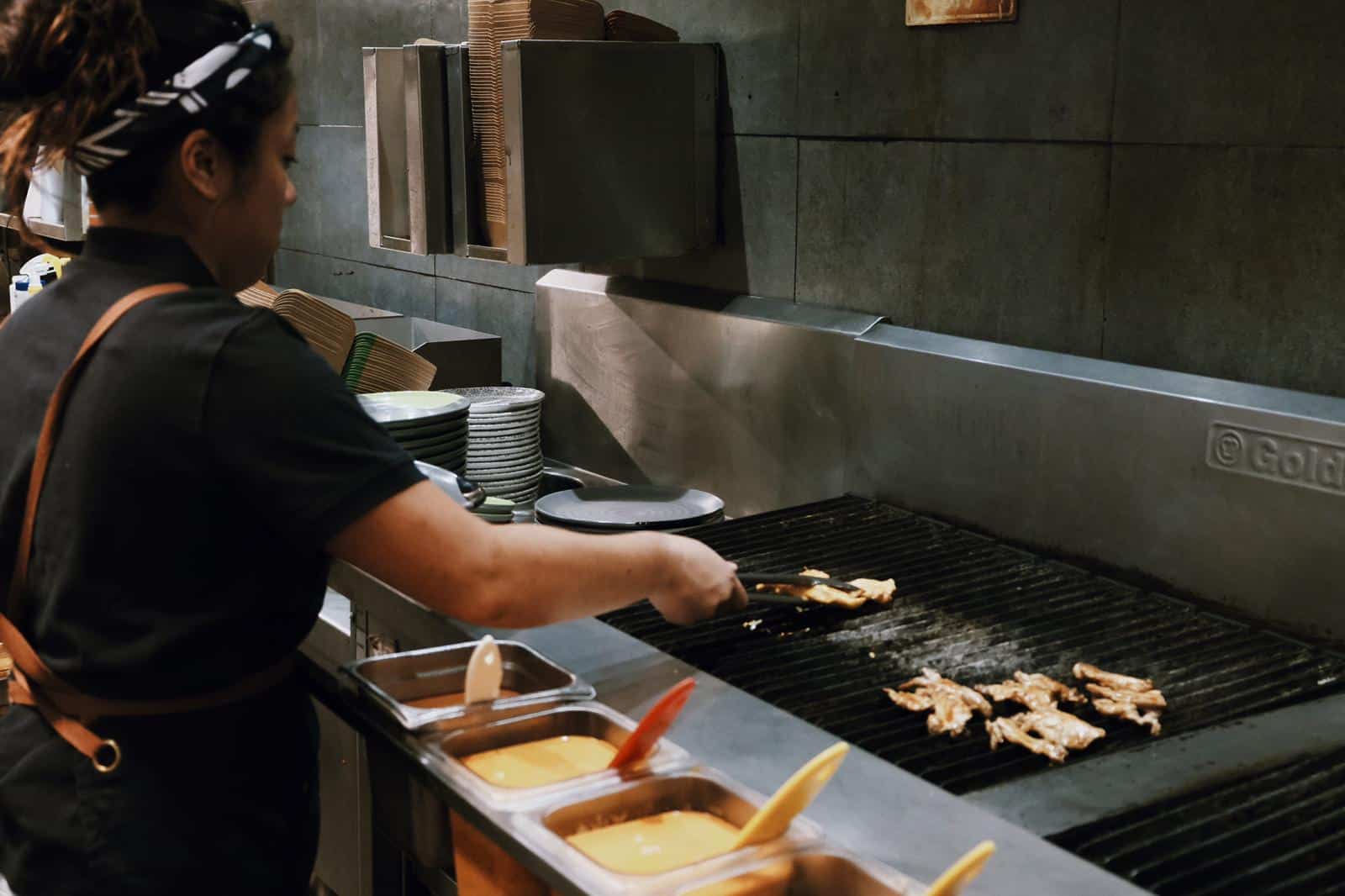
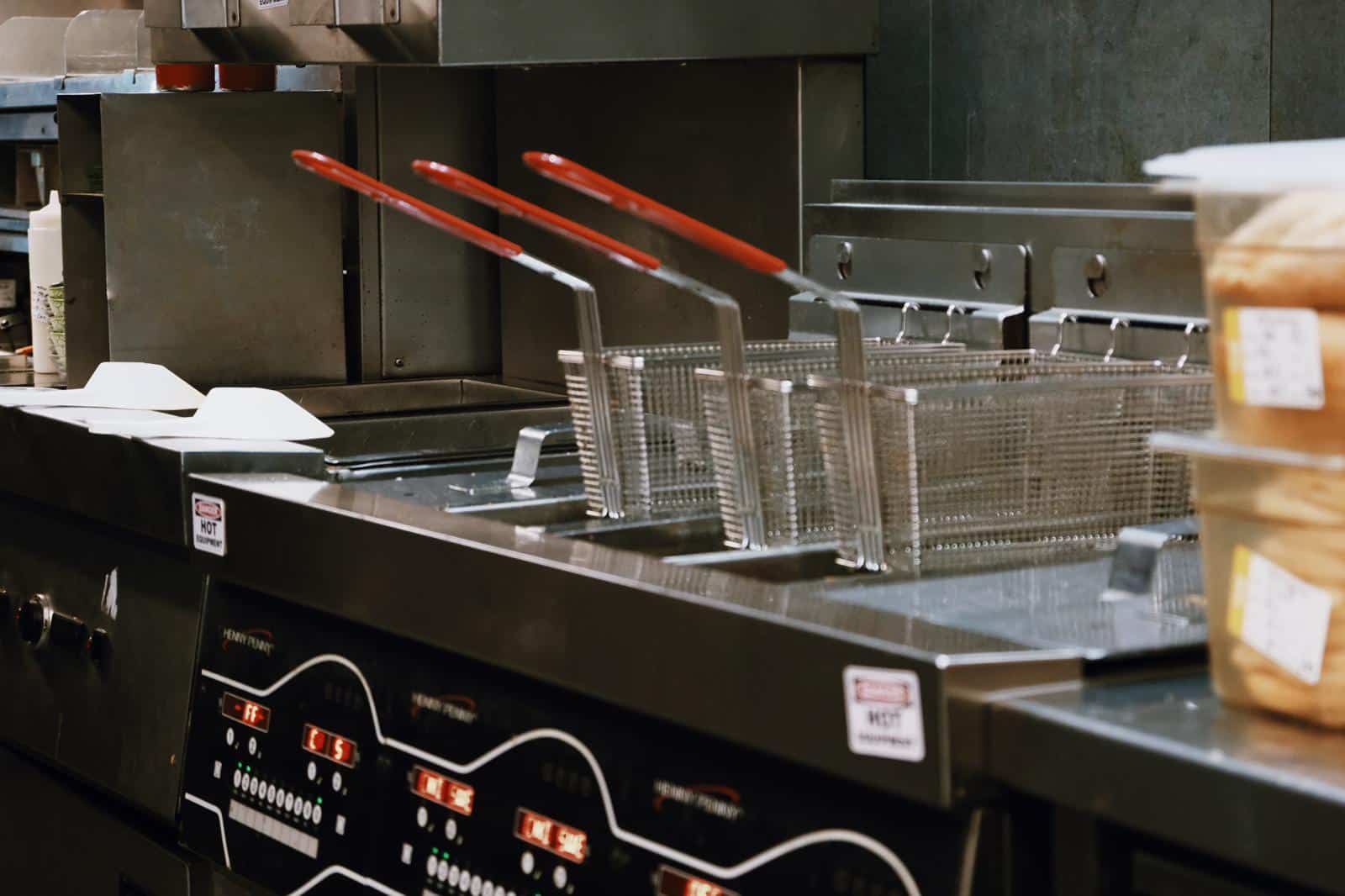
The Solution - One partner. One System. 120 Locations.
Baker Group AU was awarded the contract for the maintenance of kitchen equipment of all 120 restaurants across the country. We started by implementing a centralised maintenance system which was set up to streamline the servicing process, improving efficiency and response times for service requests across all locations.
Our close working relationships with Nando’s OEM suppliers ensured that all work carried out aligned with the stringent quality and performance benchmarks set by the manufacturer. This commitment to OEM standards ensured seamless integration, maintaining the integrity and value of Nando’s equipment.
Our close working relationships with Nando’s OEM suppliers ensured that all work carried out aligned with the stringent quality and performance benchmarks set by the manufacturer. This commitment to OEM standards ensured seamless integration, maintaining the integrity and value of Nando’s equipment.
Results - Drop in equipment maintenance costs and smoother running of 120 sites.
Nando’s achieved significant cost savings with Baker Group AU by consolidating its contractor network and eliminating multiple layers of fees. This streamlined approach not only reduced expenses but also led to improved operational efficiency. Moreover, with the same technician qualified to service all gas and electric equipment from all OEM brands, Nando’s saved on incremental labour costs.
By providing a single point of contact for all its stores, Baker Group AU enhanced communication and fostered a more cohesive and responsive network for Nando’s. This centralised model facilitated smoother interactions, faster issue resolution, and better overall co-ordination between Nando’s sites and Baker Group AU’s technicians.
At Baker Group, we prioritise quality by meticulously planning and allocating ample resources to manage our contracts effectively. For Nando’s, we ensured our service level was maintained by over-allocating technicians initially, allowing us to meet any request without compromising on service. Our focus on repairs and scheduled maintenance for Nando’s gas and electrical equipment across over 120 stores nationally ensures consistent, reliable support.
By providing a single point of contact for all its stores, Baker Group AU enhanced communication and fostered a more cohesive and responsive network for Nando’s. This centralised model facilitated smoother interactions, faster issue resolution, and better overall co-ordination between Nando’s sites and Baker Group AU’s technicians.
At Baker Group, we prioritise quality by meticulously planning and allocating ample resources to manage our contracts effectively. For Nando’s, we ensured our service level was maintained by over-allocating technicians initially, allowing us to meet any request without compromising on service. Our focus on repairs and scheduled maintenance for Nando’s gas and electrical equipment across over 120 stores nationally ensures consistent, reliable support.
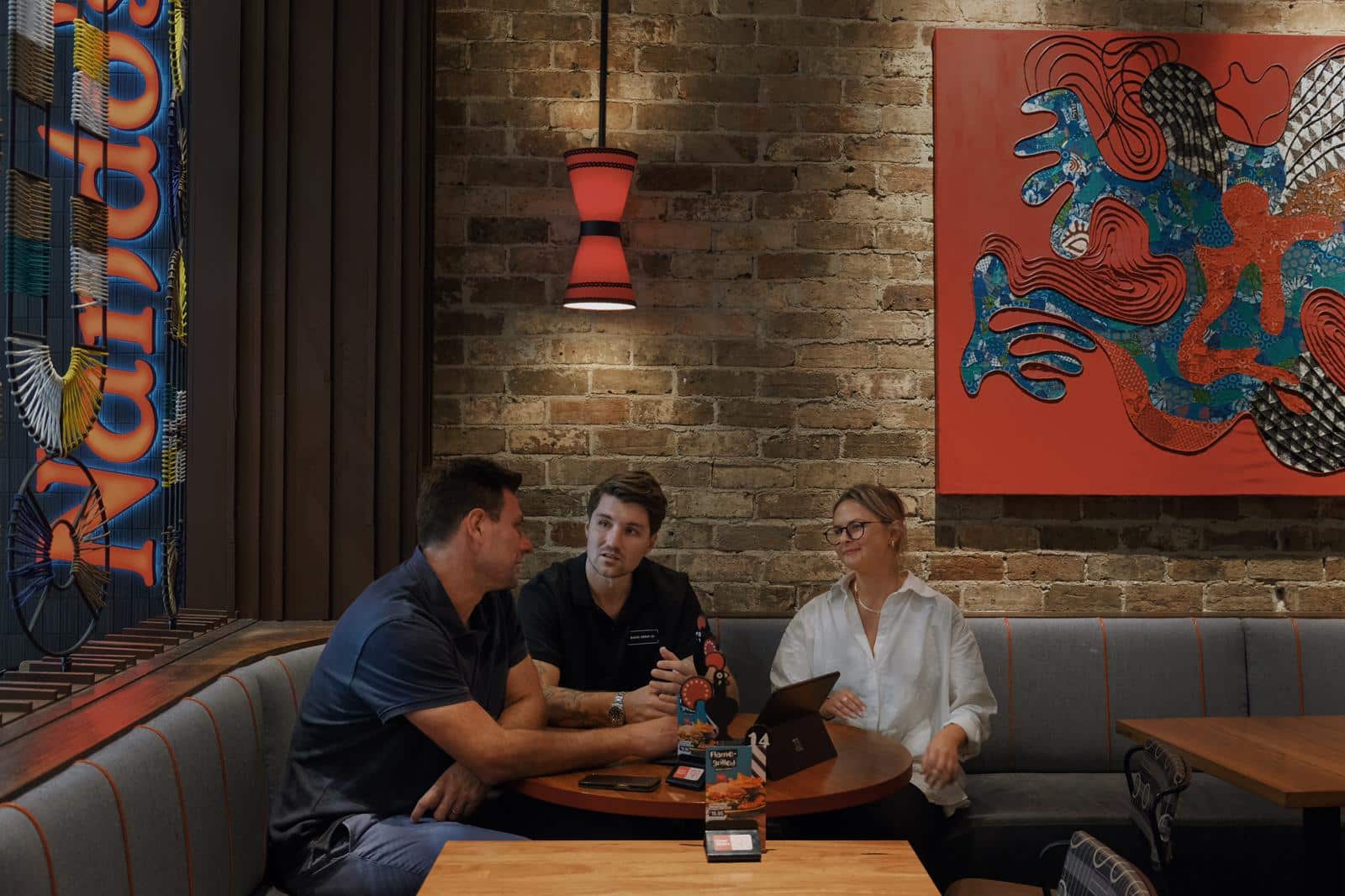
Our Commitment To Quality
We began by putting forward a plan that ensured we would have enough resources to manage the contract. As a rule, we tend to work a bit heavy in terms of resources, meaning we over-allocate technicians at the start to ensure we can meet any request without diluting our service standards. Nando’s don’t require full time, onsite support so we focus on repairs and scheduled maintenance of their gas and electrical equipment. With over 120 stores nationally, this works out to at least 2 to 3 jobs per day.
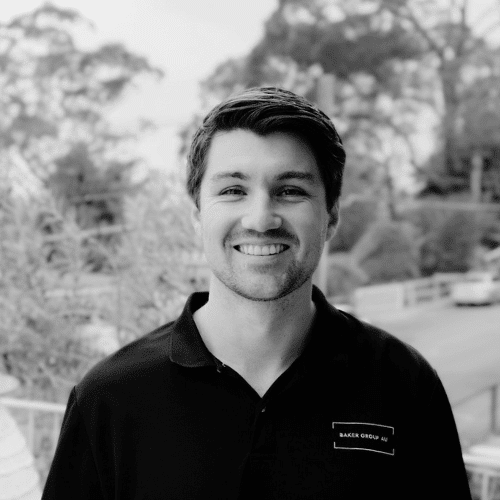
Scott Baker
Managing Director
Get in touch with us to discuss a customised maintenance plan for your commercial kitchen equipment.
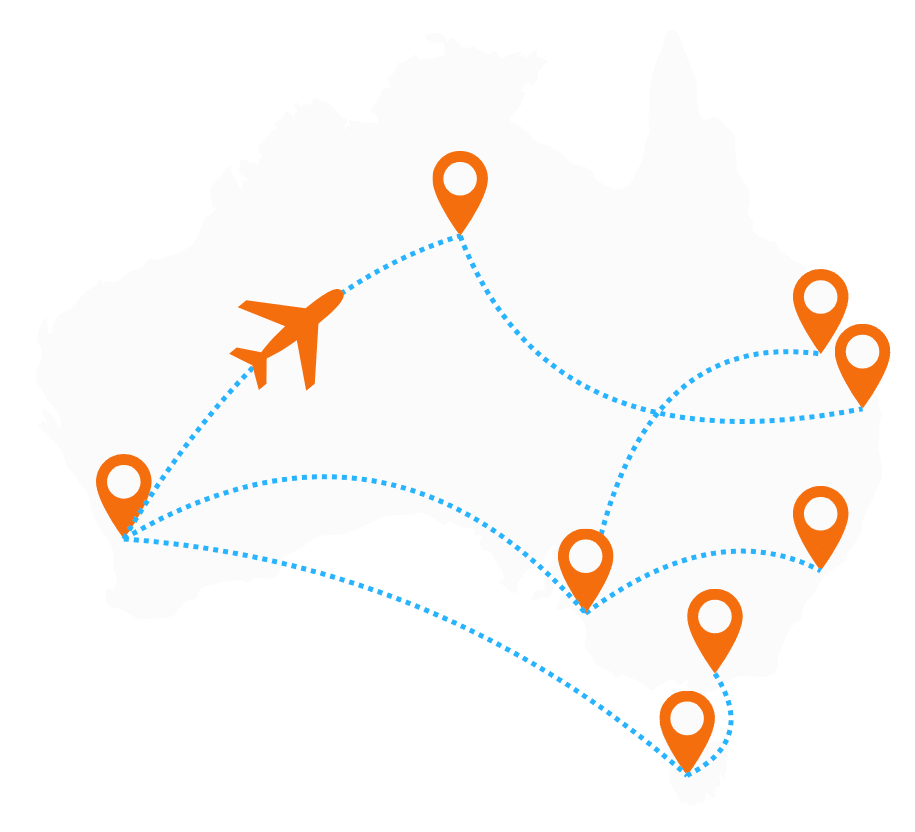